Made a new tunnel brace.
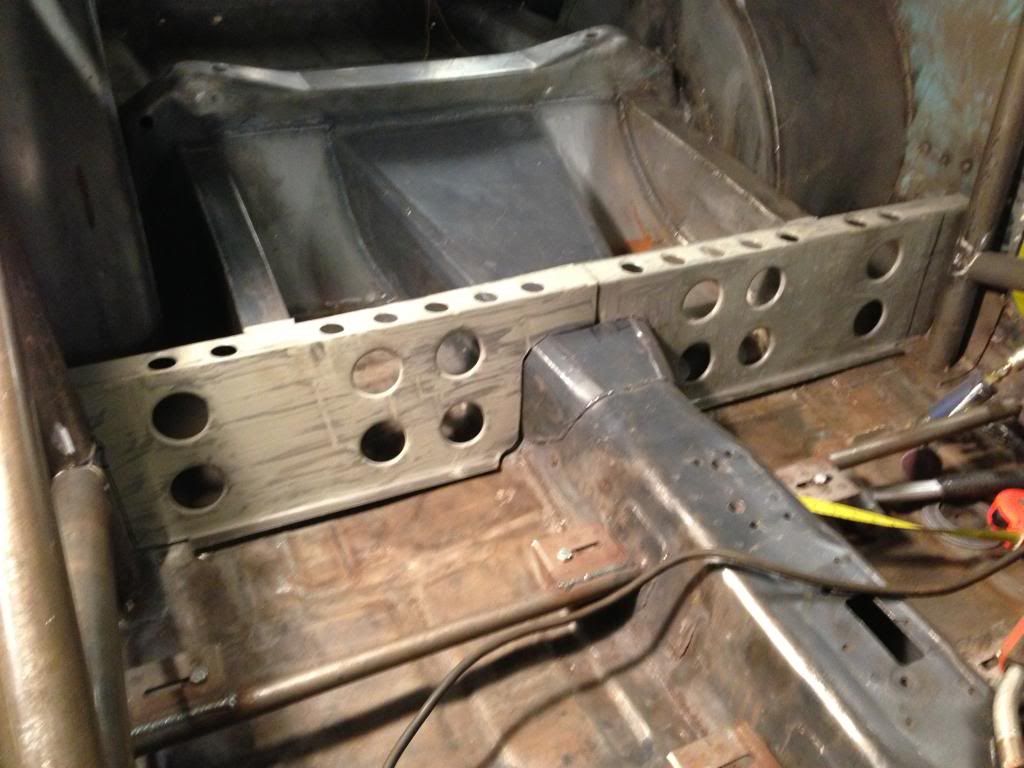
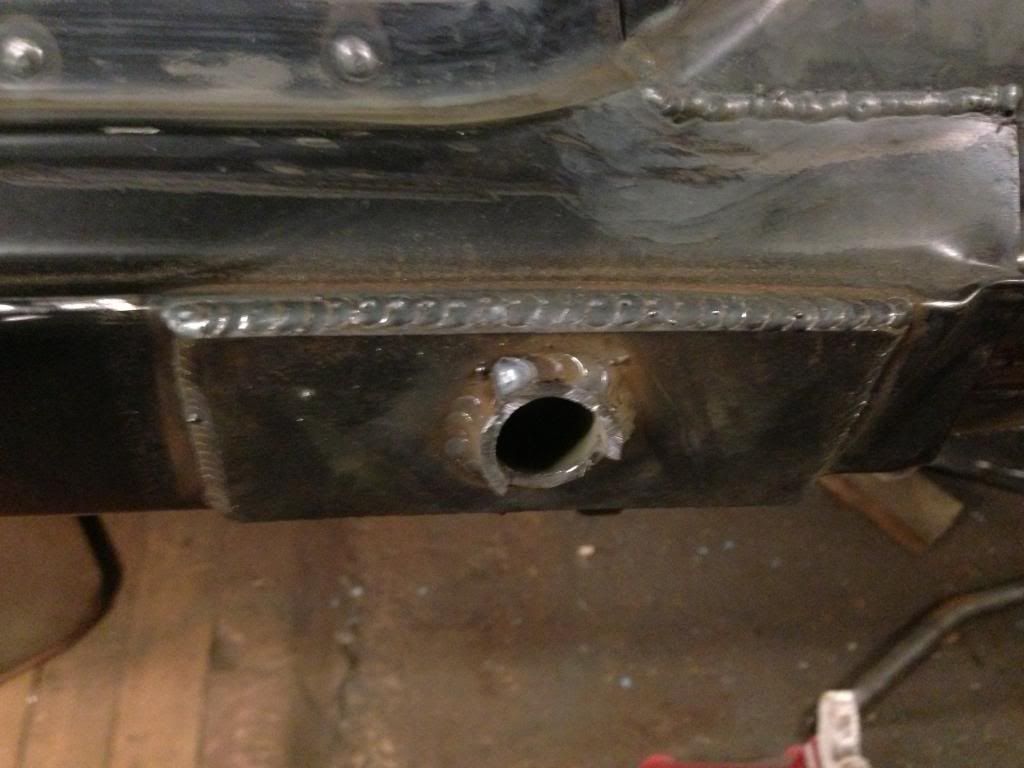
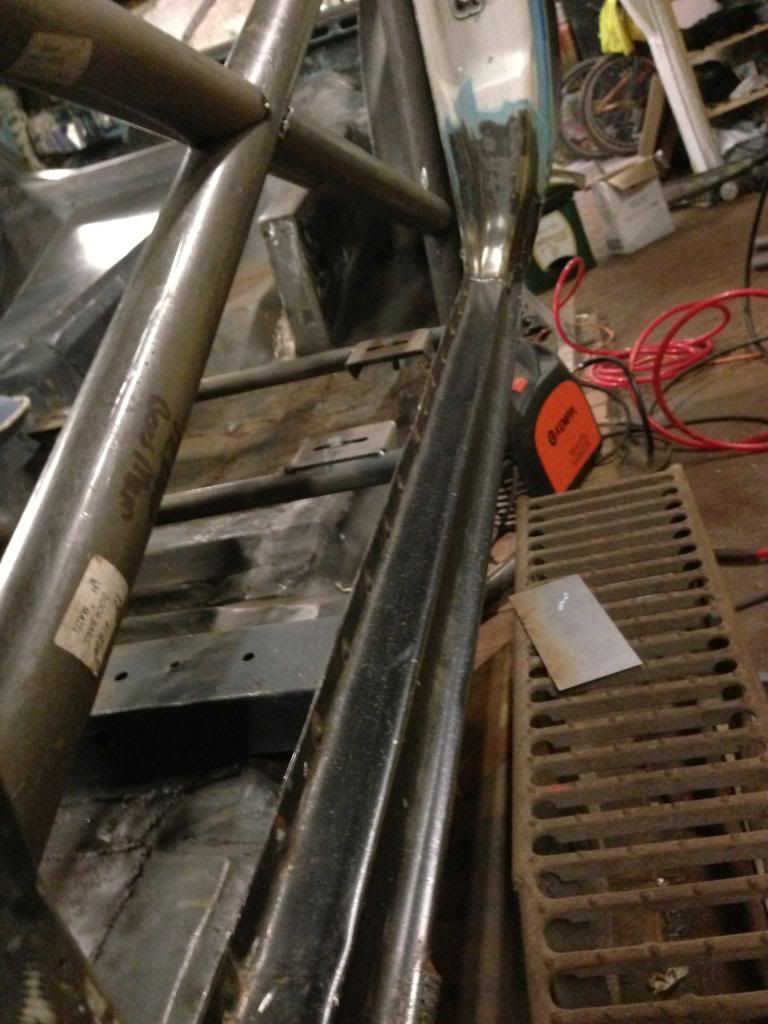
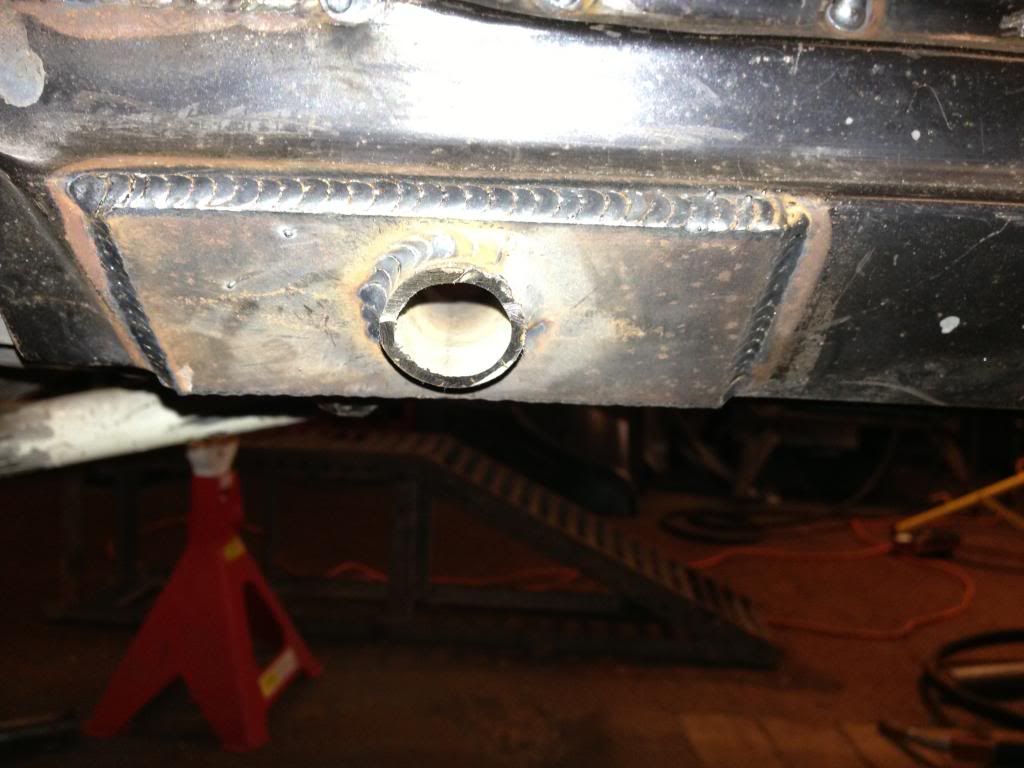
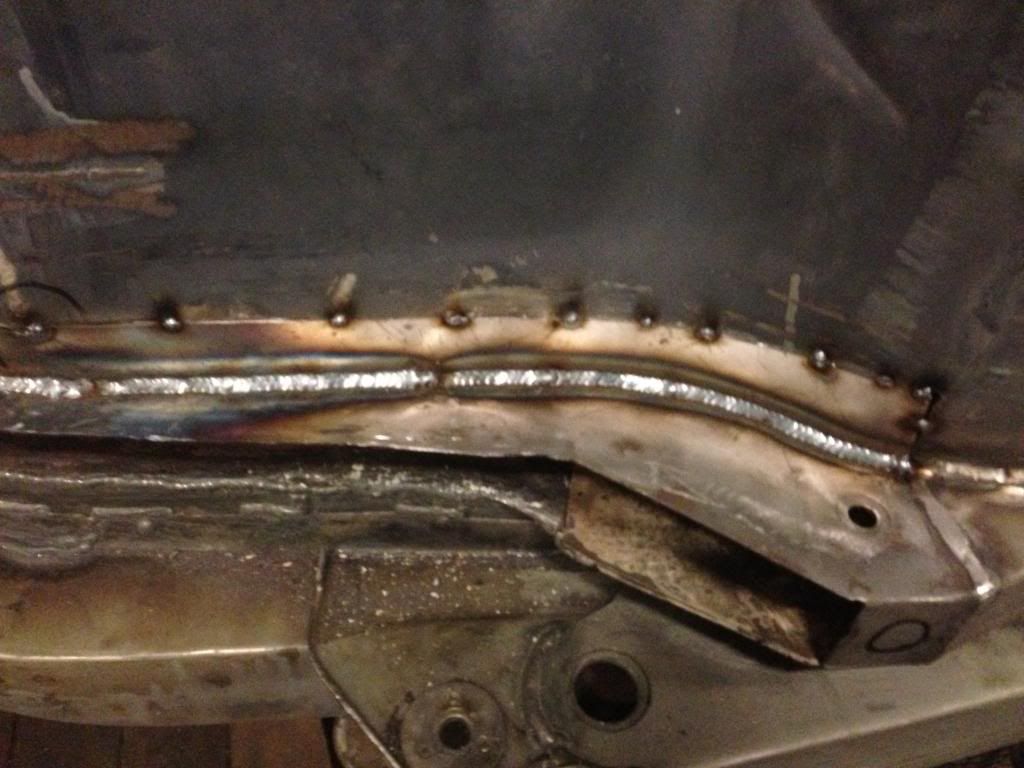
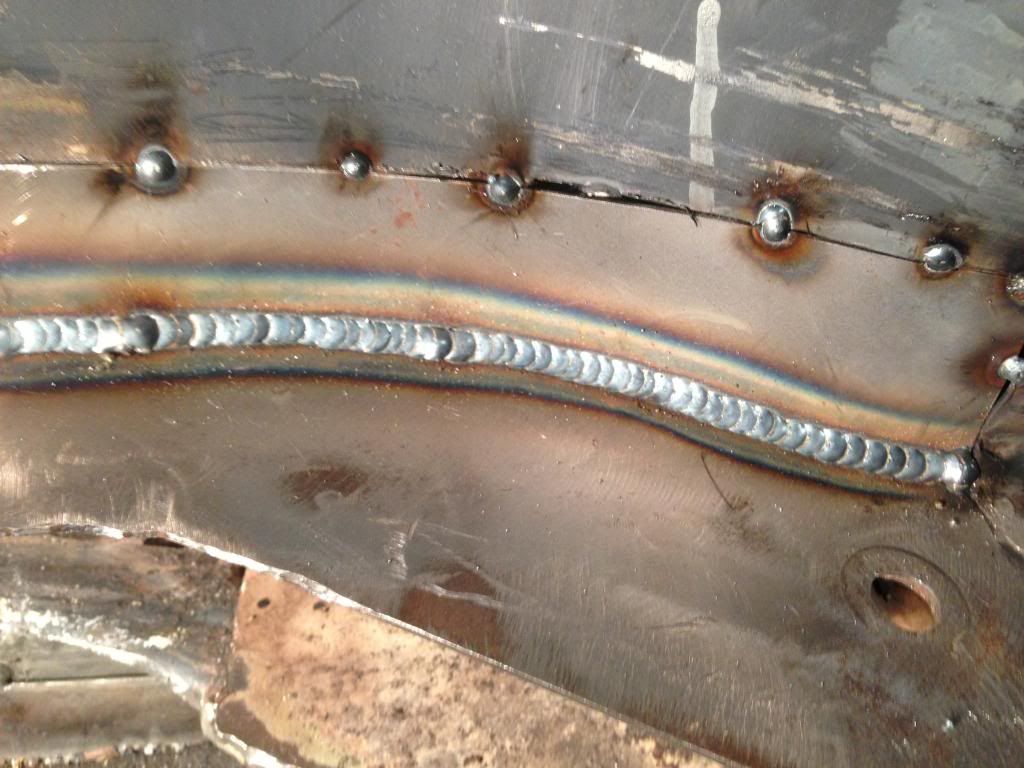

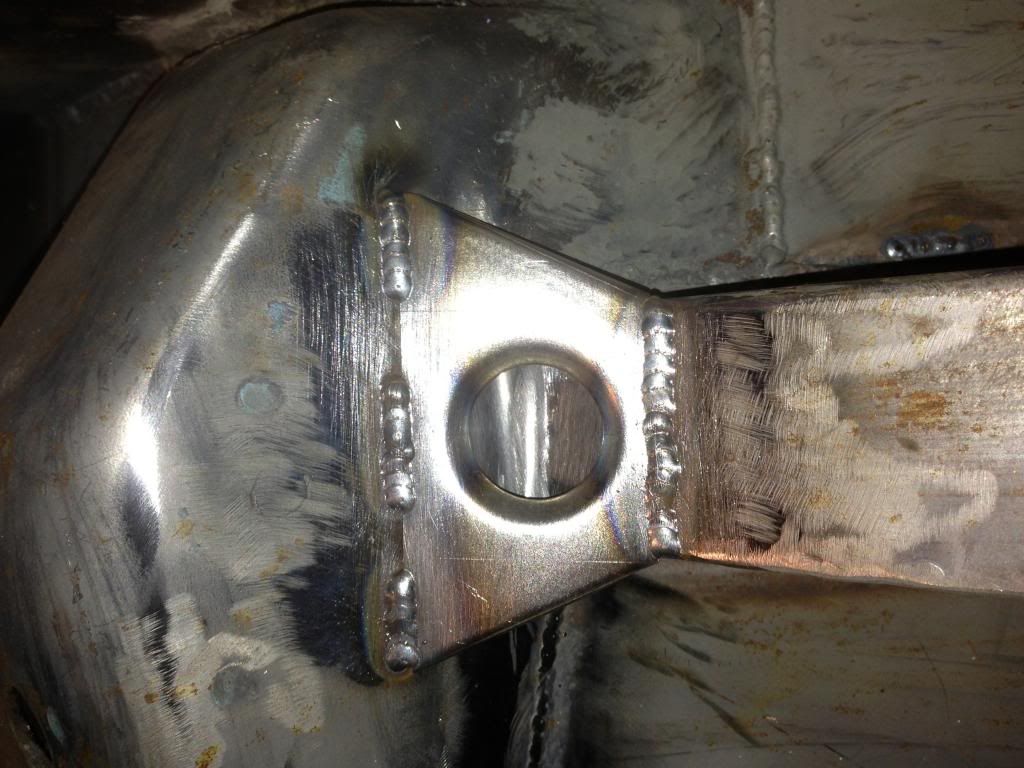

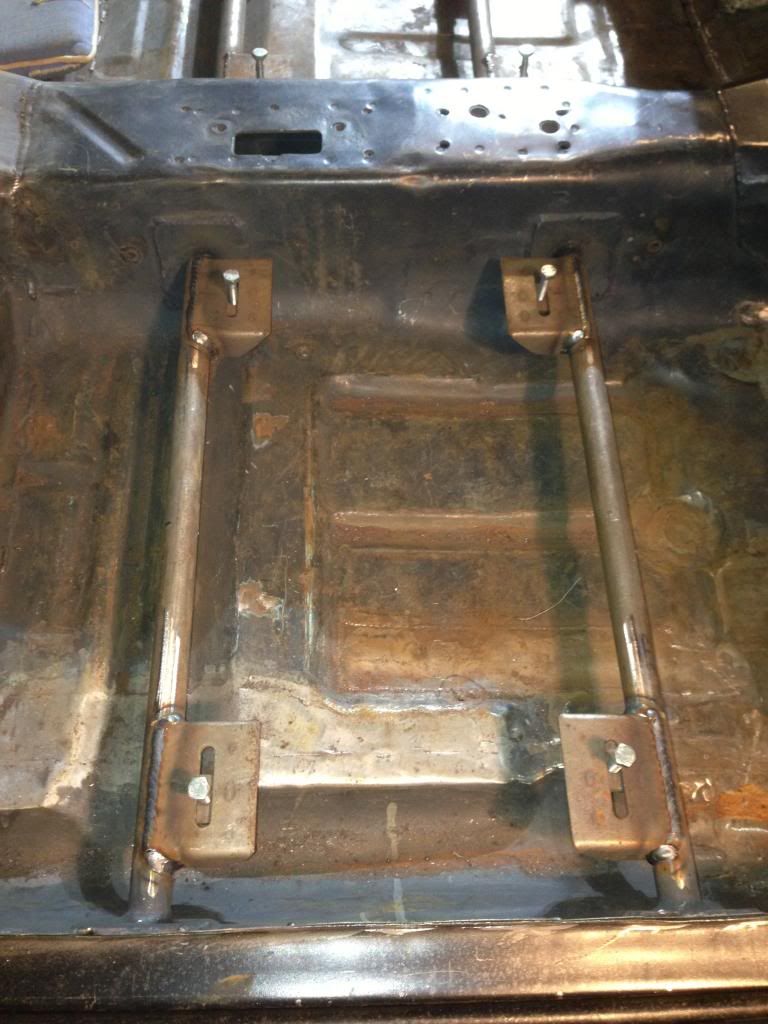
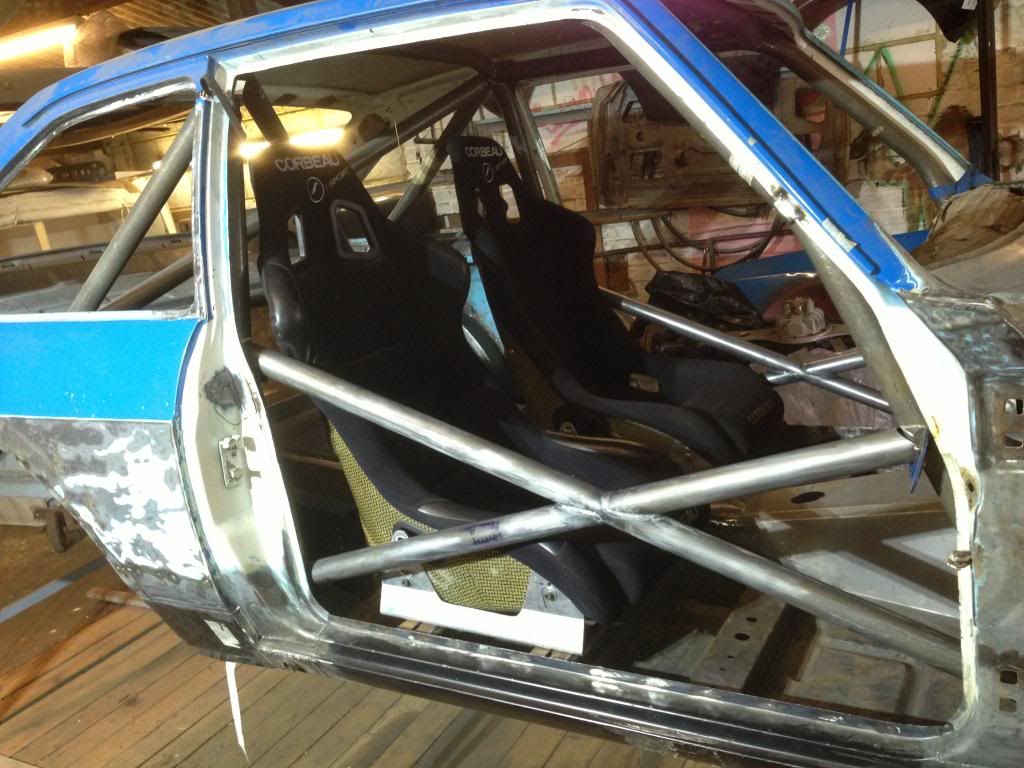
Just picked the gearbox up from having it rebuilt by Paul at first motion.
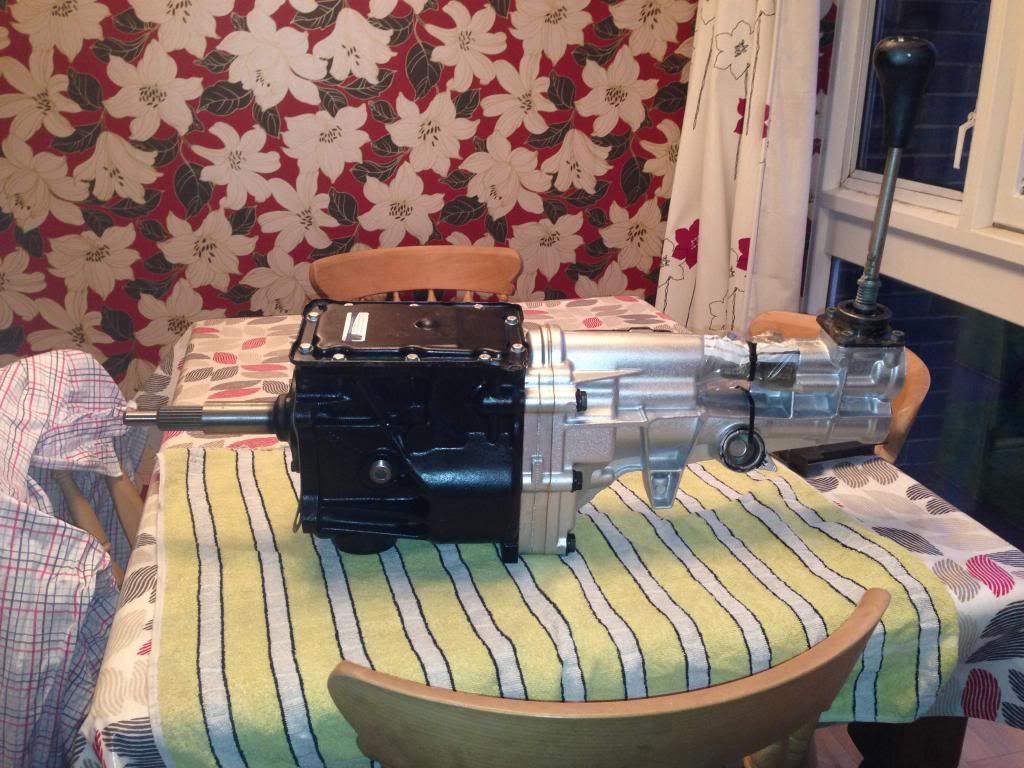
And some new rear Tarmac arches as the Forest ones didnt look right so close to the swage line because of the big rear tubs.
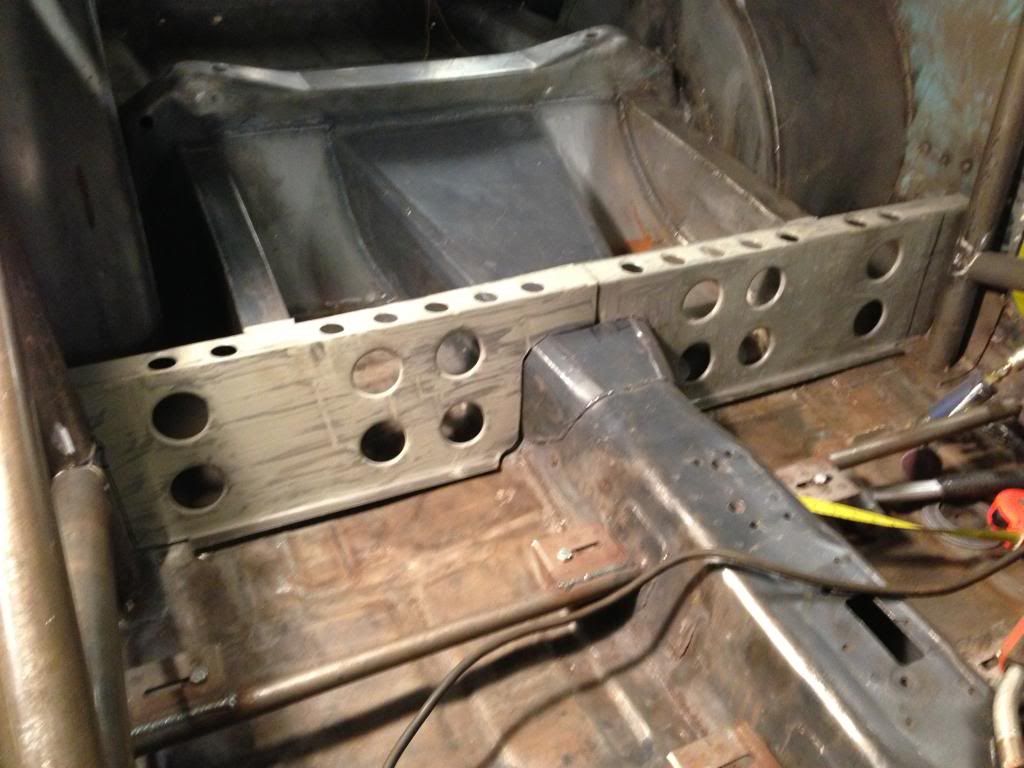
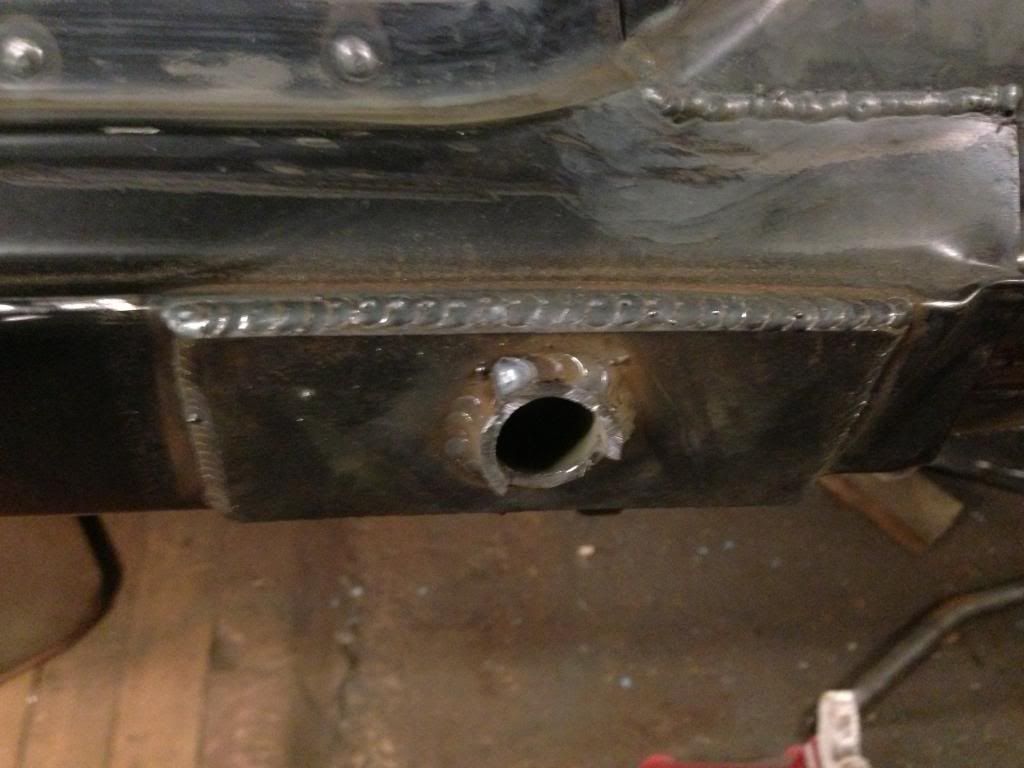
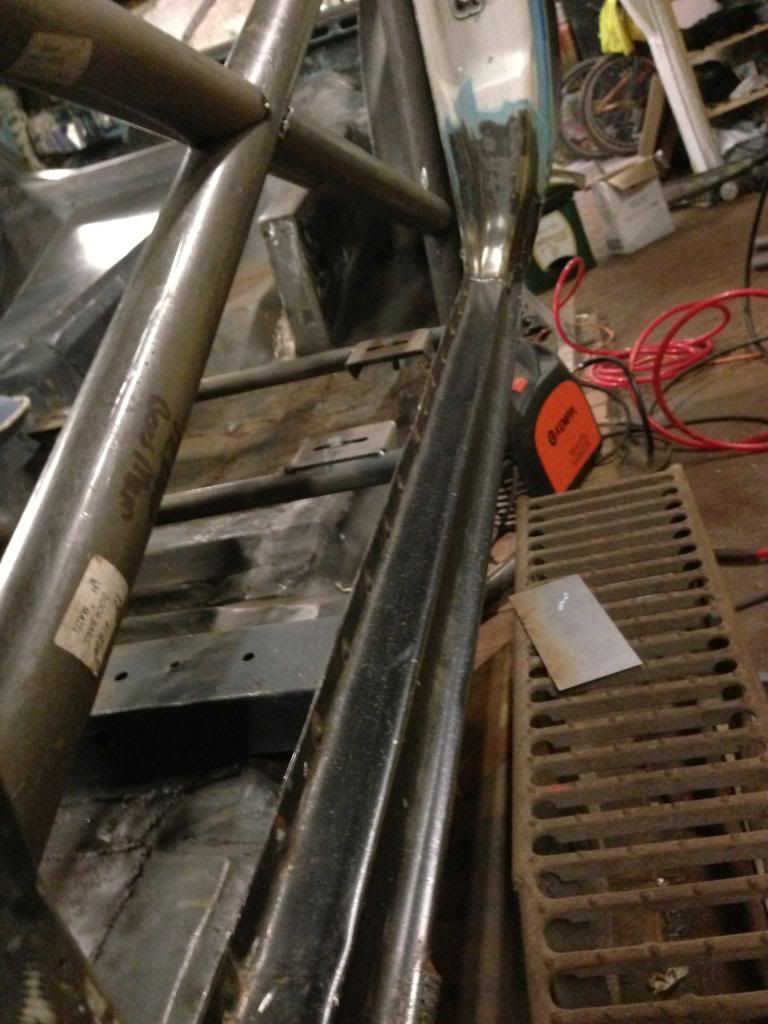
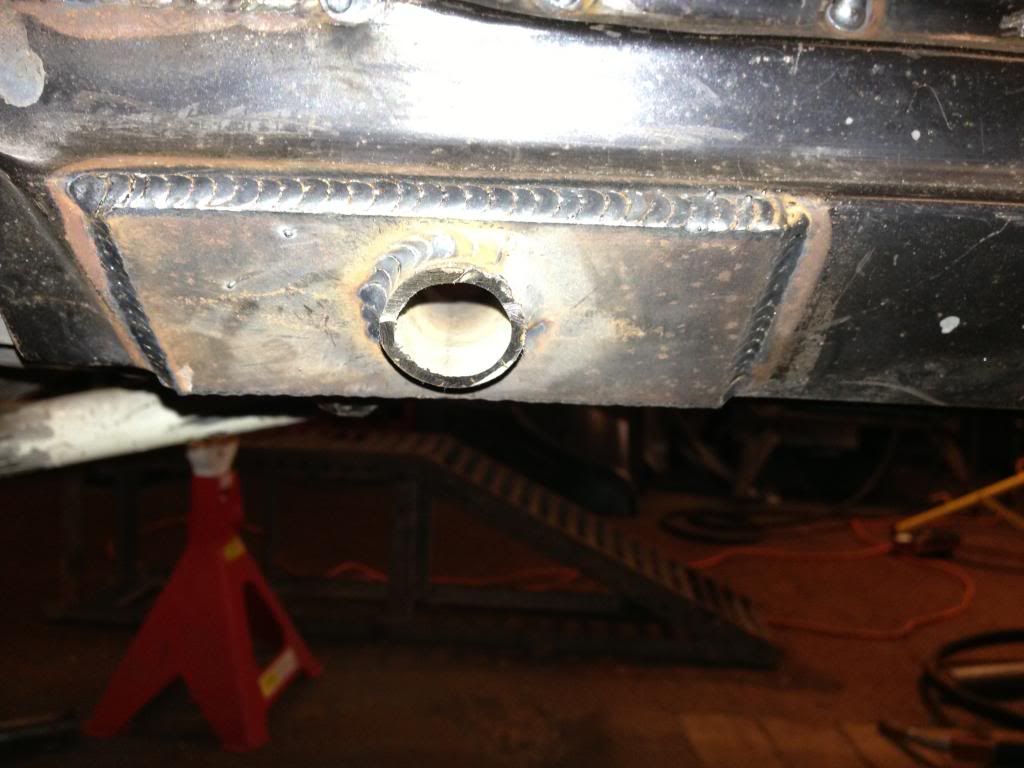
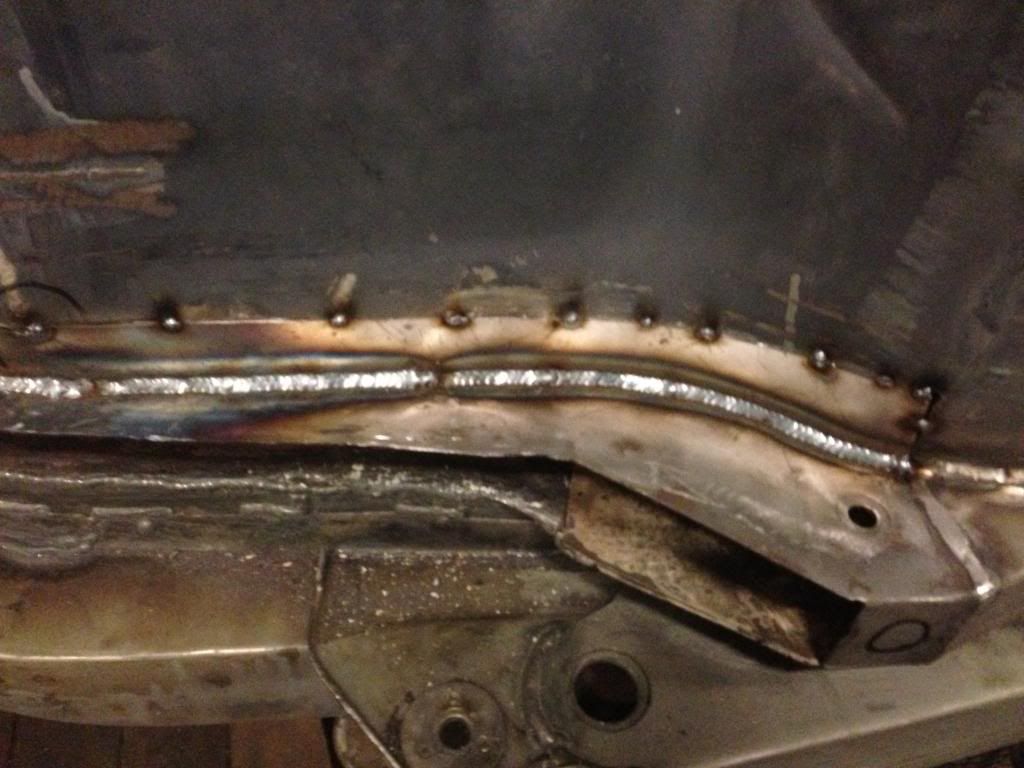
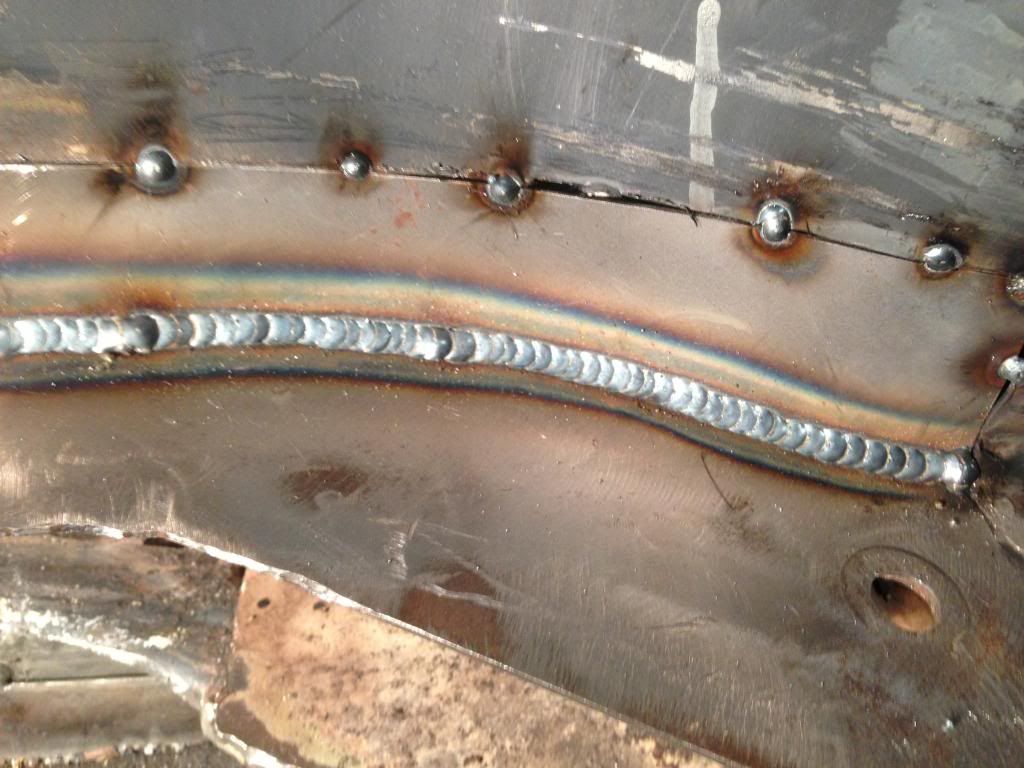

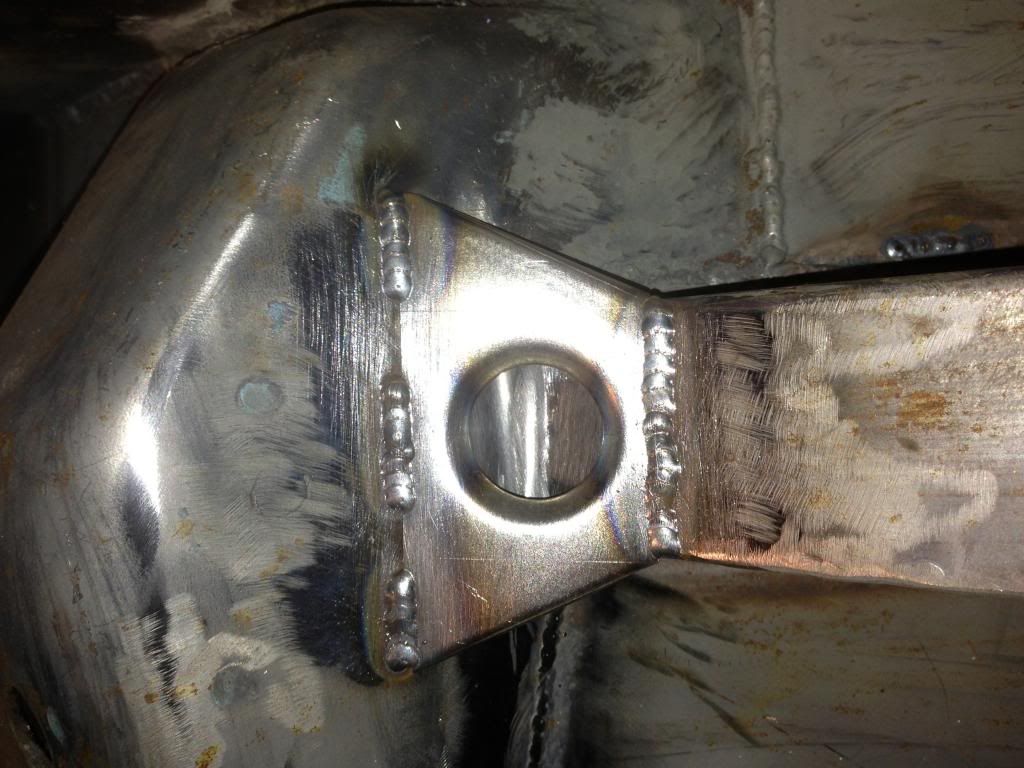

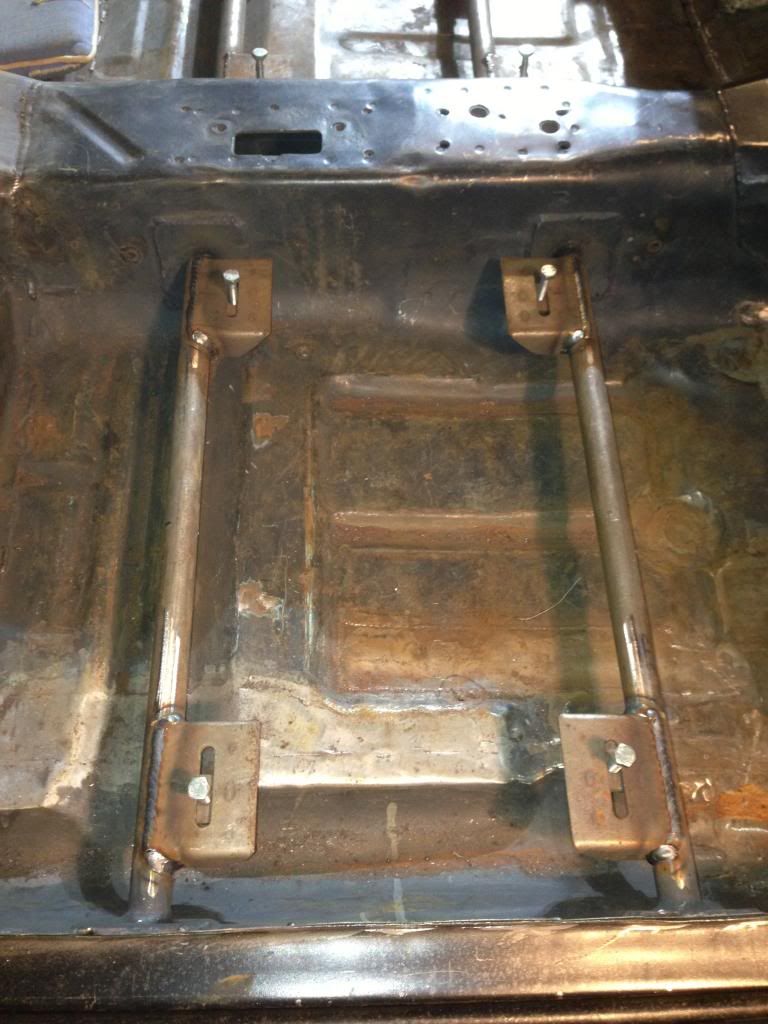
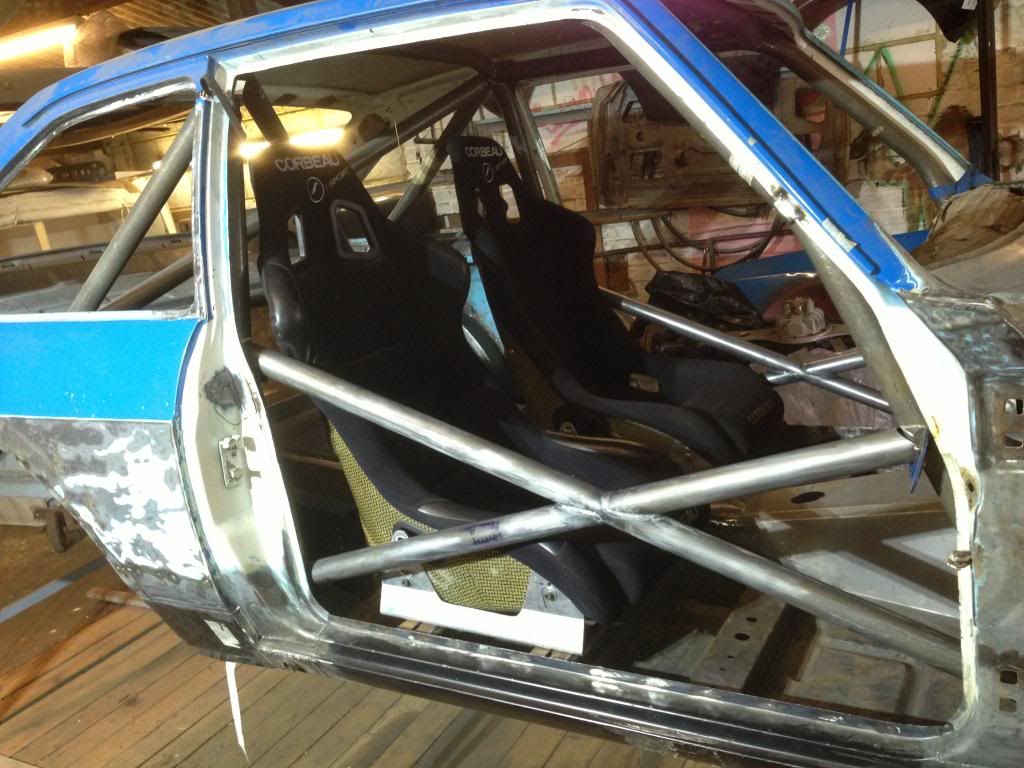
Just picked the gearbox up from having it rebuilt by Paul at first motion.
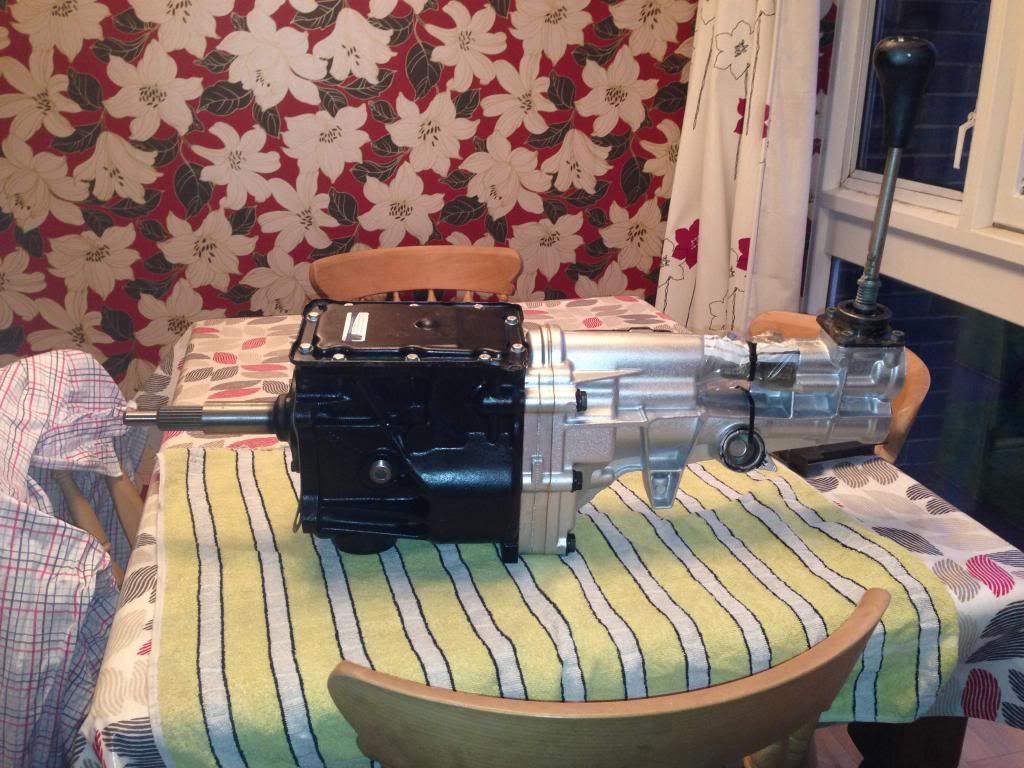
And some new rear Tarmac arches as the Forest ones didnt look right so close to the swage line because of the big rear tubs.
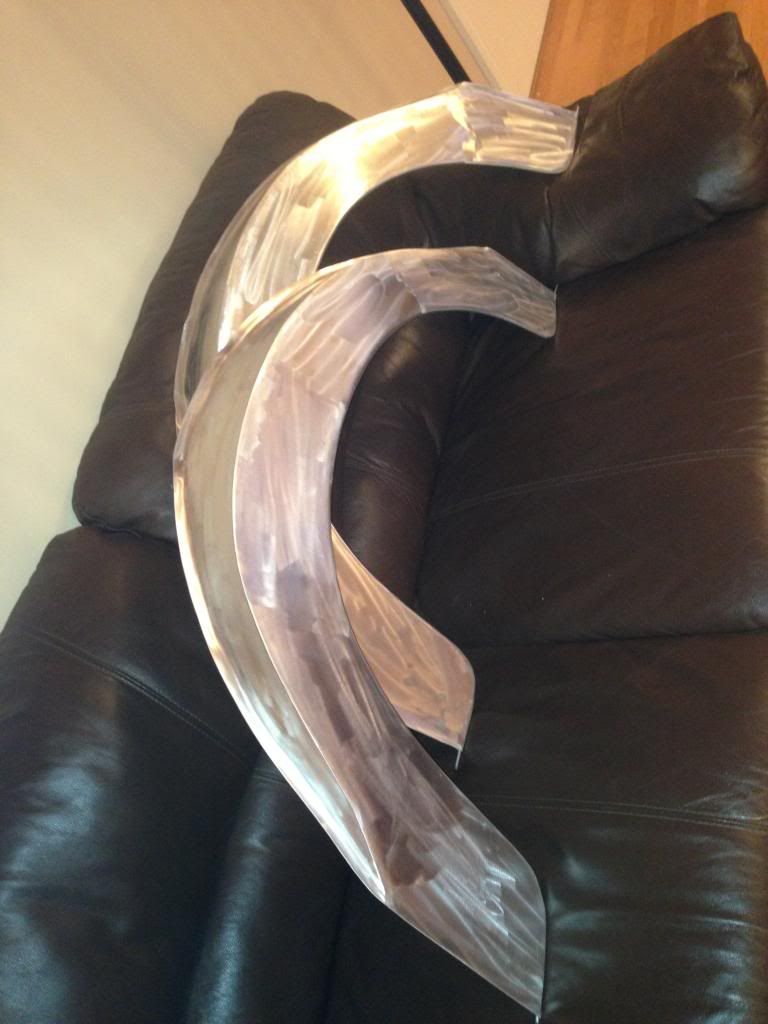
Comment